A respected maker of advanced geospatial data collection platforms, AISPECO supports the data-collection efforts companies in fields such as utilities, forestry, city mapping, mining, civil engineering, and more. The Lithuania-based company deploys multi-sensor payloads on airborne, mobile, and stationary platforms, and it incorporates lidar, hyperspectral imaging, and other imaging systems to add value, accuracy, and efficiency to data-collection operations.
To learn more about AISPECO and its approach to infrastructure inspections, Commercial UAV News spoke with company CEO Mantas Vaskela.
We discussed the economics of small sensor systems, why drones work better than traditional aircraft for corridor inspections, and what the future holds for drone-based data collection.
Commercial UAV News: What are the conventional or commonly used methods for conducting corridor inspections?
Vaskela: There are multiple ways to inspect infrastructure corridors, so let’s name them and their pros and cons. The first option is a high-flying aircraft, typically a twin-engine flying 1500ft or above, having a large lidar system peeking through a hole in the fuselage of a modified aircraft. This provides an attractive price point for lidar data; however, it has severe limitations regarding the lidar’s point density and the image resolution. Additionally, the mobilization cost for that type of aircraft is very high. If the project is not of substantial size, such as a county or multi-state project, it isn’t cost-effective for this type of aircraft.
The second option would be a helicopter. If you need inspection-grade photography, you traditionally hire a helicopter patrol with a system like Teledyne FLIR 350 or Trakka. It would fly by infrastructure and stop at the point of interest, where the operator would manually point the camera, zoom in, and calibrate into the part of interest, for example, the insulator string on the powerline. While this yields a high-quality result, the operation speed is normally very slow, resulting in extremely high costs. Additionally, stopping at each point of interest is a dangerous way to fly.
The third option would be a drone-based inspection. Drones provide an alternative to helicopter-based inspection. While slightly slower in terms of operation, a crew with a drone can arrive on the scene, fly the drone very close to the asset, and take the same high-quality photographs. The downside of this compared to helicopter patrol is the ability to reach harder-to-reach areas and also the inability to fly quickly between structures, as VLOS requirements limit this.
Commercial UAV News: What is AISPECO’s approach?
Vaskela: AISPECO proposes a fourth option for corridor inspections—multi-sensor pods tailored to specific operations, including corridor inspection. For example, we can take a couple of very high-resolution cameras with zoom lenses and couple them with high-density lidar on the same helicopter. We can use AI algorithms to auto-detect the towers for the inspection imagery while collecting dense point cloud information with a lidar system. With this type of setup, you can get 2-3mm pixel resolution, allowing the inspection to be done without stopping. This can dramatically reduce the inspection cost, increase the data quality, and increase the efficiency of data collection over the other approaches.
Commercial UAV News: What are the advantages of using drones/small sensor systems for corridor inspections?
Vaskela: Mobilization and cost would be two of the most significant advantages. When the scale is sufficiently small, drones can quickly and easily inspect smaller areas of the network. Mobilizing a drone crew is considerably cheaper than deploying a twin-engine fixed-wing aircraft and crew. If you are operating a large sensor system, you typically must own the aircraft as well because it requires modifying the fuselage by cutting a hole in the bottom. If you are a drone or a small sensor system user, you can use commercial flights and rental cars to deploy to the area of operation. The AISEPCO system is similar in that you can take the equipment on commercial aircraft and temporarily install it on any compatible aircraft without requiring modification.
Commercial UAV News: What impact does the size of an inspection operation have on what systems are used?
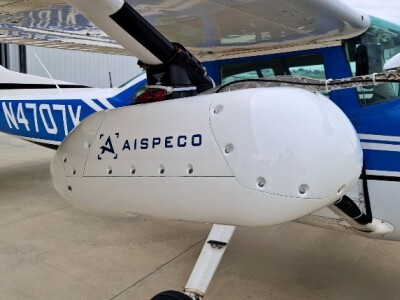
Vaskela: Regarding project size, we consider the AISPECO HELIUX LITE pod a mid-market sensor. This is larger and more expensive than a drone system equipped with a smaller sensor, but it is dramatically cheaper than large-scale systems by a factor of 3. The HELIUX LITE pod is closer to the cost of a drone system equipped for inspection than it is to a large-scale system installed inside a fixed-wing aircraft.
Drones and small sensors can become a disadvantage if the project size increases too much. It becomes too expensive to mobilize and collect projects once they are over 10 miles long. When the project sizes become hundreds or thousands of miles, the cost, time, and logistics of doing it with drones become untenable. A helicopter with a mid-market system like the AISEPCO HELIUX LITE pod can easily collect over 100 miles of utility in a single day, and a fixed-wing aircraft with the HELIUX LITE can collect 300 miles per day.
Commercial UAV News: Tell us more about AISPECO. How did you get involved in using drones for inspections? What have you learned along the way?
Vaskela: At AISPECO, we started our journey as a utility inspection company. Our first large project required us to collect front/back/nadir imagery of southern European powerlines. The first half of the project, roughly 400 miles, was done with a drone. For this project, we had the advance of beyond visual line of sight (BVLOS), and our custom-designed drone could operate for over 1 hour per flight. Despite these advantages, we collected around 20 miles daily on a good day. Some of the challenges faced on this project were local regulations and weather. It took 40 days to complete 400 miles, averaging 10 miles per day.
After this project, we started to design the early prototypes of the AISPECO system. With these systems, we were able to perform the same amount of work in just five days. While the equipment cost was substantially higher, the time savings were 800% better, making up for the additional cost. It soon became apparent that our mid-market sensor approach was far superior for this type of data collection.
Commercial UAV News: What advantages does AISPECO offer to companies and organizations involved in corridor inspections?
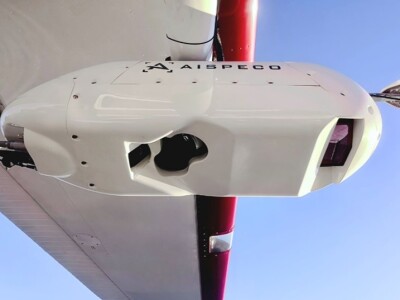
Vaskela: AISPECO was founded with the idea that your sensors should grow with you as your operations grow. This is why our pods provide the greatest flexibility of any integrated system in the market. We allow you to combine existing or new sensors in the pod to meet your data collection requirements. Our engineering team can work with you to design the perfect solution for your data collection requirements. If you need to upgrade or modify a few sensors in the system, we will help you, saving you time and money. Because the system does not require aircraft modification, you can easily reinstall the system on different aircraft in less than an hour, reducing your downtime due to aircraft maintenance.
At AISPECO, we started our journey as operators. We have experienced many of the challenges that go along with corridor inspection. We have designed our solutions to eliminate as many hurdles to quality data collection as possible to increase your efficiency, reduce your downtime, and collect the correct type of data for your projects.